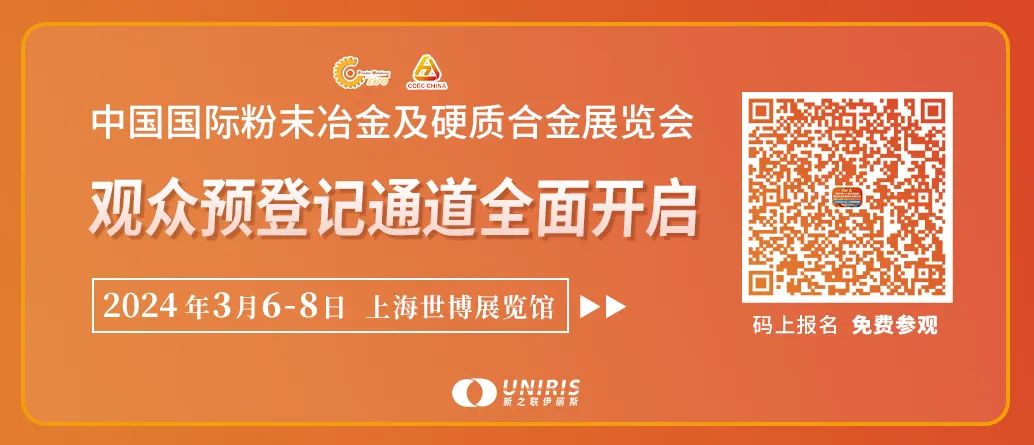
摘 要: 为了系统全面地研究高温合金盘的热成形过程,通过建立高温合金宏微观材料模型,设置热成形工艺参数和边界条件,构建了 GH2132 高温合金盘宏微观多尺度有限元模型。通过对高温合金盘热成形过程进行数值模拟,研究了高温合金盘热成形工艺过程中的宏观变形和微观组织演变行为,分析了高温合金盘热成形后的宏观变形状态和微观组织分布情况。通过进行高温合金盘热成形物理试验对数值模拟结果进行了验证。结果表明,通过数值模拟能够精确预测高温合金盘热成形工艺过程中的宏观变形和微观组织演变。
1 有限元模型构建
1. 1 GH2132 高温合金材料模型
为了准确描述 GH2132 高温合金的高温流动行为,采用图 1 所示的真应力-真应变曲线数据作为其本构关系。图 1 所示的真应力-真应变数据是按参考文献的试验方法在 Gleeble 3500 试验机上进行等温压缩试验得来的,等温压缩试验温度 850、900、950、1000、1050 和 1100 ℃,应变速率 0. 001、0. 01、0. 1 和 1 s-1。该真应力-真应变数据范围涵盖了高温合金热变形参数范围,是准确预测 GH2132高温合金宏观变形的基础。
材料的热物理参数会随着温度的变化而变化,采用随温度变化而变化的材料参数能够保证和提高数值模拟的精度。GH2132 高温合金的热传导系数、杨氏 弹 性 模 量、热膨胀系数及热容如表 1 所 示。GH2132 高温合金泊松比设置为 0. 28。
1. 2 GH2132 高温合金热成形有限元模型
1. 2. 1 高温合金盘热成形工艺过程
GH2132 高温合金盘热成形工艺如图 2 所示。热成形工艺过程主要包含加热、转运、成形和冷却4 个阶段。
加热阶段: 坯料加热过程分为两个阶段。第 1阶段将坯料以 5 ℃ ·min-1 慢速加热至 900 ℃ 并保温,使坯料温度均匀分布; 第 2 阶段将坯料以9. 5 ℃·min-1 快速加热至始锻温度 1000 ℃ 并保温,使坯料温度均匀分布。进行分梯度加热和保温是因为 GH2132 高温合金在 900 ℃时晶粒长大缓慢,900 ℃以上晶粒会较快地长大,因此选择将坯料先加热到900 ℃保温,然后通过快速加热的方式减少坯料在高温状态下停留的时间,减少晶粒尺寸的长大。转运阶段: 保温完成后对坯料进行热包套,减少热量散失,再将坯料由加热炉转运至安装在压力机上的下模,下模预热温度 380 ℃ ,转运时间约 60 s。成形阶段: 将坯料在模具中进行热成形并保压。冷却阶段: 将锻件空冷至室温。1. 2. 2 高温合金盘热成形有限元模型
GH2132 高温合金盘热成形过程存在热、力、微观组织的交互作用,有限元模型中不但需要综合考虑微观组织演变、传热和力学行为,而且需要考虑这 3 个场量相互之间的相互作用。高温合金盘坯料为直径 Φ300 mm,高度 200 mm且带 10 mm×10 mm 斜角的圆柱体,有限元模型如图3 所示。坯料和模具网格采用四面体网格。坯料设置为塑性体,初始温度 20 ℃。圆柱面和端面为加热、转运及冷却过程中与空气的热对流面,圆柱面为进行热成形时与空气的热对流面。模具设置为刚体,初始温度 380 ℃。模具所有面均为热成形过程中与空气的热对流面。
1. 2. 3 高温合金盘热成形有限元工艺参数设置
根据拟定的高温合金盘热成形工艺,设置有限元工艺参数如下。加热及保温阶段: 坯料初始温度 20 ℃,环境温度设置如图 4 所示; 此时未进行包套,GH2132 高温合金辐射率设置为 0. 5,坯料与环境的传热系数设置为 0. 02 N·s-1·mm-1·℃ -1。
转运阶段: 转运时间 60 s,此时已进行热包套,GH2132 高温合金辐射率设置为 0. 05,坯料与环境的传热系数设置为 0. 005 N·s-1·mm-1·℃ -1。成形阶段: 坯料转运完成后上模空载下行,坯料在下模上静置 20 s 后上模与坯料接触,此时上下模间距 187 mm。热成形时上模运动速度如图 5 所示,上模运动至与下模距离 27 mm 时停止运动,结束锻造过程,模具初始温度 380 ℃。坯料和模具之间的摩擦类型选择剪切摩擦,摩擦因数设置为 0. 2。
热成形时坯料进行热包套,模具和坯料接触面传热系数为 0. 5 N·s-1·mm-1·℃ -1; 保压 20 s,保压时上模运动速度 0 mm·s-1。热成形过程中功热转换系数设置为 0. 95。模具的材料选用 H13 热作模具钢,参数设置参照 DEFORM 材料库中的 AISI-H-13。模具与环境的传热系数设置为 0. 02 N·s-1·mm-1·℃ -1。
冷却阶段: 冷却时间 18000 s,GH2132 高温合金辐射率设置为 0. 5,坯料与环境的传热系数设置为 0. 02 N·s-1·mm-1·℃ -1。2 高温合金盘热成形工艺宏微观数值模拟
按 1. 2 节方法构建高温合金盘热成形工艺有限元模型并进行数值模拟。根据高温合金盘结构组成,在轮芯选择 2 个点P1、P2,在轮毂选择 2 个点 P3、P4,在辐板和轮缘各选择 1 个点 P5、P6 进行点追踪,分析高温合金盘各部位在不同阶段的微观组织演变情况。选择的点位置如图 6 所示。
2. 1 坯料加热及保温阶段数值模拟
2. 1. 1 坯料加热及保温阶段温度变化规律
坯料加热及保温阶段温度分布如图 7 所示。由图 7 可知,当炉温 ( 环境温度) 达到 900 ℃ 时 ( 图7a) ,坯料温度由初始温度 20 ℃ 提 升 至 640 ~743 ℃。此时,坯料棱边温度最高,端面和圆柱面温度次之,心部温度最低。这是由于坯料棱边在圆柱面和端面的交界处,圆柱面和端面同时发生热对流和热辐射,热对流和热辐射作用最显著,升温最快; 圆柱面和端面也和环境直接接触,也能同时进行热对流和热辐射,升温速度也较快; 心部不和环境直接接触,而是与圆柱面和端面通过热传导进行热量传递使温度升高,因此温度提升速度最慢。在 900 ℃ 下保温 120 min 后 ( 图 7b) ,坯料温度分布均匀,趋于炉温 900 ℃ 。当炉温升高至1000 ℃ 时 ( 图 7c) ,坯料温度提升至 905 ~ 945 ℃,温度分布规律和加热到 900 ℃时一致。在 1000 ℃下继续保温 60 min 后 ( 图 7d) ,坯料温度分布均匀,趋于炉温 1000 ℃。各追踪点加热保温阶段温度演变情况如图 8 所示。

由图 8 可知,位于坯料棱边附近的 P2 和 P4 点对加热响应速度最快,温度升高最快,临近圆柱面的 P6 点次之,位于心部的 P2、P3 和 P5 点加热响应速度最慢。在环境温度升高期间,各位置温度升高速度呈先上升再下降的趋势,这与炉温和坯料各位置的温差有关系,温差和坯料升温速度呈正相关关系。刚开始加热时,炉温和坯料温差较小,坯料温度上升较慢; 随着炉温快速升高,炉温和坯料温差逐渐增大,坯料温度快速升高; 当坯料升温速度大于炉温升高速度时,温差减小,坯料温度逐渐降低; 当开始保温时,炉温不再增加,随时间推移温差显著减小,坯料温度上升速度也随之显著减小。
2. 1. 2 坯料加热及保温阶段平均晶粒尺寸变化规律
坯料加热及保温阶段坯料平均晶粒尺寸分布如图 9 所示。坯料初始平均晶粒尺寸为 32 μm。由图可知,当环境温度达到 900 ℃ 时 ( 图 9a) ,坯料温度较低,受热时间较短,坯料各部位平均晶粒尺寸保持在 32 μm,未出现晶粒长大。在 900 ℃ 下保温120 min 后 ( 图 9b) ,坯料经历较长时间保温,平均晶粒尺寸长增大至 34. 5 ~ 35. 4 μm,出现了较小程度的晶粒长大现象。且坯料棱边平均晶粒尺寸最大,端面和圆柱面平均晶粒尺寸次之,心部平均晶粒尺寸最小。这和坯料温度分布情况相对应,棱边升温最快,处于更高温度下,晶粒长大幅度最大; 而端面和圆柱面温度、心部温度相对较低,晶粒长大幅度依次降低。当炉温达到 1000 ℃时 ( 图 9c) ,坯料平均晶粒尺寸提升至 34. 8 ~ 35. 8 μm,由于快速加热时间较短,坯料平均晶粒尺寸有微小幅度的上升。在 1000 ℃ 下继续保温 60 min 后 ( 图 9d) ,坯料平均晶粒尺寸提升至 62. 2 ~ 74. 2 μm,相 对 于 炉 温900 ℃时有较大幅度升高,晶粒在高温状态下快速长大。由以上分析可知,当采用分段加热方案时,在晶粒缓慢长大的 900 ℃ 环境条件下进行保温以获得均匀温度,显著减少了坯料的温度梯度及在高温( 1000 ℃ ) 下的保温时间,降低了坯料晶粒在高温下的速率。

加热及保温阶段坯料平均晶粒尺寸演变情况如图 10 所示。由图 10 可知,开始加热时,坯料温度较低,未出现晶粒长大现象,当加热 10560 s 后,在 900 ℃下保温时,坯料各位置晶粒才开始出现晶粒长大现象。和坯料温度演变情况相对应,P2 和P4 点的平均晶粒尺寸增长最快,P6 点次之,P1、P3 和 P5 点也出现了一定的晶粒长大,但晶粒长大速度最慢。
2. 2 坯料转运阶段数值模拟
2. 2. 1 坯料转运阶段温度变化规律
转运至成形工位后坯料温度分布如图 11 所示。由图可知,当坯料转运完成后,坯料棱边温度降低最为明显,为 931 ℃ ; 端面和圆柱面温度降低次之,心部温度几乎无变化。坯料棱边热对流和热辐射最明显,温度降低最快; 圆柱面和端面也和环境直接接触,也能同时进行热对流和热辐射,降温速度也相对较快; 心部与圆柱面和端面进行热传导,由于转运时间较短,心部温度变化幅度极小。
转运过程中坯料各追踪点温度演变情况如图 12所示。转运前初始状态坯料温度范围 931 ~ 1000 ℃。在转运过程中,位于坯料棱边附近的 P2 和 P4 点温度降低速度最快,临近圆柱面的 P6 点也有所降低
但温度降低速度相对于 P2 和 P4 点慢,位于心部的P1、P3 和 P5 点受外界温度影响小,温度仅有小幅度降低。2. 2. 2 坯料转运阶段平均晶粒尺寸变化规律
坯料转运至成形工位后的平均晶粒尺寸分布如图 13 所示。坯料转运完成后,坯料平均晶粒尺寸由62. 2~74. 2 μm 小幅度增大至 62. 9 ~ 74. 4 μm。由于转运时间较短且坯料各位置温差较小,平均晶粒尺寸整体分布规律与转运前一致: 坯料棱边平均晶粒尺寸最大,端面和圆柱面平均晶粒尺寸次之,心部平均晶粒尺寸最小。
坯料转运至成形工位过程中各追踪点平均晶粒尺寸演变情况如图 14 所示。由图可知,在转运过程中,各追踪点平均晶粒尺寸近乎按线性方式增长,平均增长幅度 0. 2 ~ 0. 7 μm。转运过程中,坯料平均晶粒尺寸仍保留了加热过程中的不均匀性: 越靠近坯料心部,平均晶粒尺寸越小。
2. 3 热成形阶段数值模拟
2. 3. 1 坯料热成形阶段变形规律
坯料在热成形过程中等效应变分布如图 15 所示。由图可知,随着上模的运动,坯料开始受到挤压发生变形,轮毂的凸台首先完成充型,然后轮芯的凸台逐步完成充型,材料继续往辐板和轮缘流动,最终形成飞边。在热成形过程中,材料从中心向四周流动,等效应变也由中心向四周逐渐增大。热成形后,锻件内部发生了较大的变形。轮芯心部、轮毂心部、辐板和轮缘等位置效应变较大且均匀,但轮芯凸台和轮毂凸台位置等效应变较小。

热成形过程各跟踪点等效应变演变情况如图 16所示。由图可知,在热成形过程中,位于高温合金盘轮毂的 P3 和 P4 点率先发生了材料流动,等效应变增大; 随后,位于轮芯、辐板和轮缘的 P1、P5和 P6 点开始发生热变形; 最后,位于高温合金盘轮芯凸台的 P2 点开始发生变形。热变形过程中,各位置开始发生变形后等效应变呈逐渐上升趋势。当热变形完成后,位于轮芯心部、轮毂心部、辐板和轮缘等位置的 P1、P3、P5 和 P6 点等效应变达到较高水平,位于轮芯凸台和轮毂凸台位置的 P2 和P4 点材料主要发生整体位移,材料流动较少,等效应变较小。2. 3. 2 坯料热成形阶段温度变化规律
坯料热成形过程温度分布如图 17 所示。由图可知,当进行热包套的坯料与下模接触后,与模具发生接触传热,接触面温度快速降低。当模具继续下行时,坯料和模具接触面温度继续降低,当完成热成形时,坯料表面最低温度为 902 ℃。

在热成形过程中,锻件发生变形且不与模具接触的位置温度出现了不同程度的升高。当完成热成形时,坯料心部最高温度达到了 1010 ℃。这是由于在热成形过程中上模将对坯料做功,所做的功的一部分转换成热量储存于坯料内部,导致锻件温度升高。锻件发生变形且不与模具接触的位置通过做功积攒了大量的热量,温度显著升高。其他区域虽然通过变形积攒了一些热量,但坯料与模具接触面存在热交换,温度会有一定程度降低。在保压过程中,上模不再对锻件继续做功,锻件温度不再上升,此时锻件表面和上下模接触面积达到最大,接触换热更加剧烈,因此锻件温度在保压过程中快速降低。保压完成后,锻件温度已由保压前的 902 ~ 1010 ℃降低至 874~1000 ℃。热成形过程中各跟踪点温度演变情况如图 18 所示。由图可知,在成形过程中,随着成形的进行,坯料温度呈现两种不同趋势。在锻件内部的 P1、与其他区域的热传导和热辐射继续进行,温度出现降低趋势。在锻件表面附近轮芯、轮毂凸台位置的P2 和 P4 点温度逐渐降低,这也是由于完成变形后无持续的热量供应以维持较高的温度。在保压阶段,锻件各位置温度均以较快的速度逐渐降低。
2. 3. 3 坯料成形阶段平均晶粒尺寸变化规律
热成形过程坯料的动态再结晶体积分数分布如图19 所示。由图可知,在模具下行过程中,变形部位陆续达到临界应变并发生动态再结晶,且动态再结晶体积分数越来越大。当变形完成时,轮芯心部、轮毂心部、辐板和轮缘等位置均发生了完全的动态再结晶,轮芯凸台、轮毂凸台由于发生了较大的刚性位移,虽也发生了动态再结晶,但属于不完全的动态再结晶。

热成形过程坯料的动态再结晶体积分数演变情况如图 20 所示。可以看出,在热成形过程中,位于高温合金盘轮毂的 P3 点率先发生了变形和动态再结晶,动态再结晶体积分数迅速升高,随后位于轮芯、辐板和轮缘的 P1、P5 和 P6 点也开始发生变形和动态再结晶。最终,位于锻件轮芯心部的 P1 点、轮毂心部的 P3 点、辐板的 P5 点和轮缘的 P6 点的动态再结晶体积分数均为 100%或接近 100%。P4 点虽然也较早地发生了材料流动,但等效应变较小,但在变形初期未达到临界应变,未发生大规模的动态再结晶,最终动态再结晶分数达到约 40%,而位于高温合金盘轮芯凸台的 P2 点开始发生变形时间较晚且等效应变较低,最终动态再结晶体积分数仅为约 15%。
热成形过程中平均晶粒尺寸分布如图 21 所示。在热成形过程中,随着模具的下行,坯料逐步开始发生变形,应变增加,达到发生动态再结晶的临界条件发生动态再结晶,形成新的细小均匀的晶粒,晶粒尺寸显著降低。当变形完成时,发生完全动态

再结晶的轮芯心部、轮毂心部、辐板和轮缘等位置晶粒细小均匀,最小晶粒尺寸达到 1. 18 μm。轮芯凸台、轮毂凸台发生的动态再结晶体积分数相对较低,平均晶粒尺寸最大,可达到 72. 1 μm。当保压30 s 后,动态再结晶形成的细小晶粒在短时间内有小幅度长大,最小晶粒尺寸增加至 1. 41 μm。热成形过程坯料平均晶粒尺寸演变情况如图 22所示。在热成形变形过程中,位于高温合金盘轮毂的 P3,位于轮芯、辐板和轮缘的 P1、P5 和 P6 点以及位于轮毂和轮芯凸台区域的 P4 和 P2 点依次发生了变形和动态再结晶,平均晶粒尺寸降低。最终,动态再结晶体积分数为 100% 或接近 100% 的 P1、P3、P5 和 P6 点平均晶粒尺寸降低至较低水平,而P2 和 P4 点动态再结晶体积分数较低,平均晶粒尺寸仍维持在较高水平。
在热成形过程中,由于热成形持续时间较短,虽然在较高的温度下,但晶粒未发生明显的长大。但由图可知,晶粒长大引起的平均晶粒尺寸增加可抵消少量非持续动态再结晶引起的平均晶粒尺寸降低,造成平均晶粒尺寸演变曲线的小幅度波动。在保压过程中,位于锻件表面附近的 P2 和 P4点温度已较低,低于 900 ℃,晶粒几乎不长大,平均晶粒尺寸维持稳定。位于锻件内部的 P1、P3、P5 和 P6 点温度较高,平均晶粒尺寸有小幅度近线性增加。2. 4 锻件冷却阶段数值模拟
2. 4. 1 锻件冷却阶段温度变化规律
锻件空冷过程中的温度分布如图 23 所示。由图可知,在锻件空冷过程中温度迅速降低,当空冷600 s 后,锻 件 温 度 降 至 581 ~ 799 ℃,当 空冷18000 s 后,锻件温度降至 24. 9 ~ 29 ℃。空冷过程中,锻件温度由高温合金盘中心向四周逐渐降低,锻件各部位的心部温度高于锻件表面温度。
锻件空冷过程中各追踪点温度演变情况如图 24所示。由图可知,在锻件空冷过程中,锻件上各追踪点温度逐渐降低至接近室温,且随着空冷时间的增加,锻件和环境温度温差逐渐减小,锻件冷却速度逐渐降低。
2. 4. 2 锻件冷却阶段平均晶粒尺寸变化规律
锻件空冷过程中的平均晶粒尺寸分布如图 25 所示。在锻件空冷 600 s 后,发生动态再结晶的区域的亚稳态动态再结晶晶粒有微小长大,后续由于温度远低于晶粒长大所需的温度,晶粒不再长大,晶粒尺寸不再变化。空冷过程中平均晶粒尺寸整体分布规律与热成形完成后一致。
锻件空冷过程中的平均晶粒尺寸演变情况如图26 所示。由图可知,在空冷初期,除 P2 和 P4 点外的其他点由于温度较高,平均晶粒尺寸仍有小幅度升高。随着空冷的继续进行,温度进一步降低,平均晶粒尺寸保持稳定不变。空冷完成后,P2 和 P4 点平均晶粒尺寸较大,而其他位置平均晶粒尺寸较小,小于10 μm。最终各点的平均晶粒尺寸与动态再结晶体积分数密切相关,动态再结晶体积分数越大,最终的平均晶粒尺寸就越小。最终轮芯凸台和轮毂凸台区域动态再结晶体积分数较低,在高温下的长大晶粒和细小的动态再结晶晶粒同时存在,属于混晶状态。
3 数值模拟结果验证
按照高温合金盘热成形工艺进行了 GH2132 高温合金盘的热成形试验获得了高温合金盘锻件。将成形的高温合金盘进行剖切,得到高温合金盘剖切断面如图 27 所示。按照图 6 对应的 P1 ~ P6 点位置在高温合金盘上进行取样和金相试验,如图 27 所示,对高温合金盘微观组织进行验证。
由图 6 和图 27 对比可知,数值模拟获得的锻件形状和实际物理试验得到的锻件形状具有很高的相似度,说明数值模拟精确预测了锻件热成形过程中的宏观变形。对高温合金盘实物取样进行金相试验获得的金相照片如图 28 所示。由图可知,在高温合金盘 P1、P3、P5 和 P6 点的微观组织细小且均匀,无未发生动态再结晶的变形大晶粒,动态再结晶充分。P2 和P4 点晶粒大小相间,均匀性相对较差,尺寸较大的晶粒为在高温成形过程中长大后的晶粒,尺寸较小的晶粒为动态再结晶晶粒,表现为混晶组织。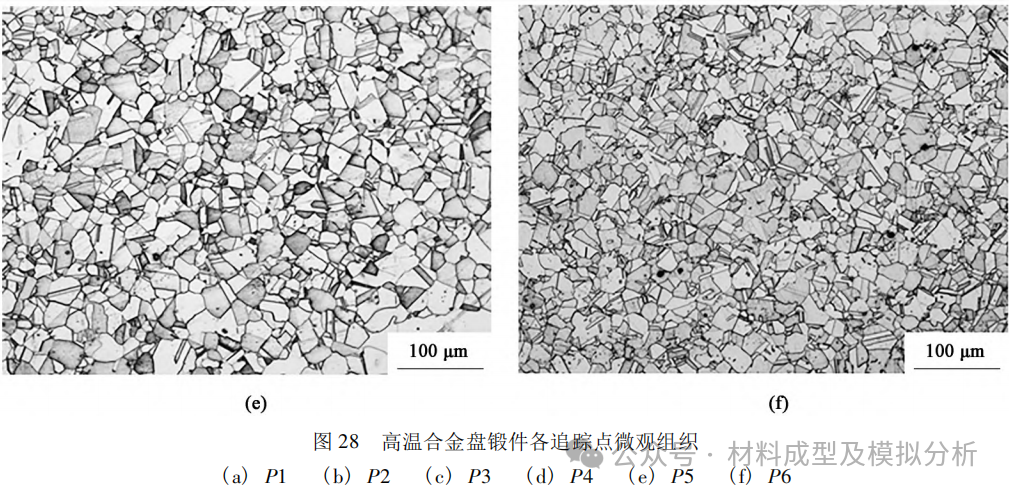
统计出各追踪点的平均晶粒尺寸分布如表 2 所示。由表 2 可知,P1、P3、P5 和 P6 点晶粒尺寸细小,在 5. 41~9. 05 μm 范围内,显著小于初始晶粒尺寸 32 μm,可认定为发生了完全动态再结晶。P2和 P4 点未发生完全的动态再结晶,微观组织中能够观察到细小均匀的动态再结晶晶粒环绕于未发生动态再结晶的变形大晶粒周围,平均晶粒尺寸分别为 59. 35 和 43. 62 μm,明显高于初始晶粒尺寸,形成混晶组织。
由表 2 可知,各追踪点位置数值模拟的平均晶粒尺寸和实际锻件的平均晶粒尺寸较为接近。各追踪点数值模拟的平均晶粒尺寸相对于实际锻件的平均晶粒尺寸最大相对误差仅为 12. 56% ( P2 点) ,平均误差仅为 7. 61%。较小的最大相对误差和平均误差说明高温合金盘锻造工艺过程微观组织数值模拟不但能充分反映实际工艺过程的微观组织演变规律,而且具有较高的精度。4 结论
(1)通过建立 GH2132 高温合金材料模型,设置工艺参数和边界条件,构建了高温合金盘宏微观多尺度有限元模型。
(2)通过构建的有限元模型,对高温合金盘在成形过程中的热-力-微观组织进行了数值模拟,研究了高温合金盘在成形过程中的宏观变形和微观组织演变。
(3)通过进行高温合金盘热成形试验对高温合金盘数值模拟过程数值模拟结果进行了验证。结果表明,数值模拟能够充分反映实际工艺过程的宏观变形和微观组织演变规律,且具有较高的精度。
文章引用:石晓玲,余新平,王继伟等.高温合金盘热成形工艺多尺度数值模拟及验证[J].塑性工程学报,2023,30(12):31-46.声 明:文章内容来源于石晓玲 材料成型及模拟分析。仅作分享,不代表本号立场,如有侵权,请联系小编删除,谢谢!